Kilka słów wstępu, czyli twarde statystyki.
Raport za rok 2019, opublikowany przez Międzynarodową Federację Robotyki (IFR),1 przyniósł pozytywne informacje dla polskiego rynku. Liczba pracujących w Polsce robotów przemysłowych wynosi 15 800 i stale rośnie. Najwięcej pochłonął ich przemysł motoryzacyjny, bo aż 37%. Statystyki te pokazują, że prędzej czy później większość z nas, pracujących w przemyśle, stanie oko w ramię z robotem.
Czy roboty zabiorą nam pracę?
W 2015 roku serwis BBC opublikował coś à la horoskop, gdzie użytkownicy za pomocą wyszukiwarki mogli wpisać nazwę swojego zawodu, by przekonać się o ryzyku jego automatyzacji. Horoskop wskazywał, że profesja urzędnika w banku lub na poczcie była zagrożona automatyzacją aż w 97%! Powiedzenie, że coś musi nabrać mocy urzędowej nabrałoby praktycznego znaczenia gdybyśmy tą mocą zasilili… roboty? Nauczyciele i wykładowcy mogli odetchnąć z ulgą – w ich przypadku ryzyko automatyzacji wynosiło tylko 3%. Autorzy badań przyjęli bardzo prosty algorytm: im bardziej praca jest powtarzalna i rutynowa, a mniej kreatywna i wymagająca umiejętności negocjacji, tym większy wykazywała potencjał do jej zautomatyzowania.
Zwiększenie bezpieczeństwa w wyniku wykluczenia czynnika ludzkiego z procesu produkcji/pracy,2 to jedna z większych zalet robotyzacji. Abstrahując od oczywistych wad i zalet, przejdźmy do wymagań technicznych.
Układ aplikacji z robotem
Norma PN-EN ISO 11161 określa wymagania bezpieczeństwa dla zintegrowanych systemów produkcyjnych, które zawierają dwie lub więcej połączone ze sobą maszyny do konkretnych zastosowań, na przykład produkcji lub montażu części. Wykaz wytycznych technicznych rozpoczyna się od rysunku (poniżej) – przykładu konfiguracji elementów na stanowisku zrobotyzowanym.
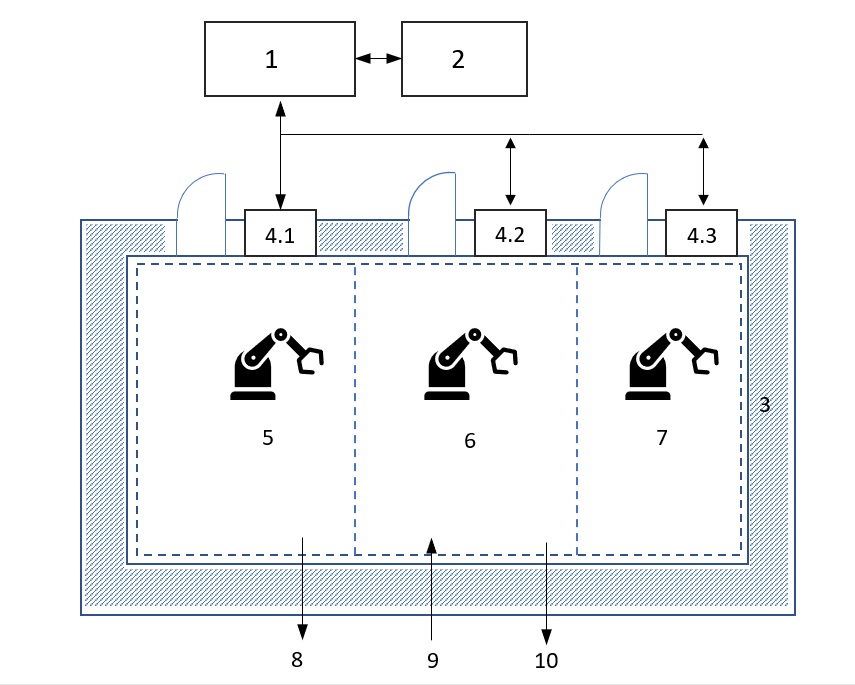
1, 2 – sterowanie nadrzędne; 3 – przestrzeń chroniona; 4.1, 4.2, 4.3 – sterowanie lokalne; 5, 6, 7 – wydzielone strefy zagrożenia; 8, 9, 10 – transport materiału
Omówmy kilka wybranych kwestii dotyczących bezpieczeństwa celi zrobotyzowanej.
Osłony
Ogrodzenie komory znajduje się po zewnętrznej stronie przestrzeni chronionej.4 Dystans pomiędzy ogrodzeniem i przestrzenią ograniczoną robota najczęściej wynika z normy PN-EN ISO 13857, która podaje odległości bezpieczeństwa uniemożliwiające sięganie do stref niebezpiecznych, tj. takie minimalne odległości, w których element niebezpieczny nie będzie mógł zostać osiągnięty w danych warunkach.
Podane wymiary5 nie budziłyby większych wątpliwości, gdyby nie uwaga w dolej części tabeli, informująca o tym, że szczelina szersza niż 18 cm umożliwia dostęp całym ciałem. Na tym etapie nadal nie ma w tym nic enigmatycznego. Zgodnie z zasadą – niezgłoszony problem nie istnieje.
Ale my lubimy zagadki. Zaprzeczeniem powyższej wytycznej jest wymóg równorzędnej normy B1 tj. PN-EN ISO 11161,6 która pozwala zwiększyć szczelinę pod ogrodzeniem do 20 cm, o ile to nie pozwoli nam na swobodne sięganie do elementów niebezpiecznych. Na którą wielkość się zdecydować?
Dwie równorzędne, wykluczające się w tej samej kwestii normy powodują, że możemy wybrać dowolną z nich. Ocena oceną, a ryzyko niezgodności z prawem rośnie proporcjonalnie do ilości środków ochronnych i konieczności ich ewaluacji.
Kontrolery
Etap, który możemy zrobić bardzo łatwo i bardzo źle. Sterowanie lokalne powinno być poza obszarami stref zagrożenia. Wokół kontrolerów nie powinny występować szczeliny umożliwiające sięganie do elementów niebezpiecznych. W praktyce, jak pokazuje poniższy przykład, sterowanie lokalnie pełniące funkcję osłony bardzo często nie spełnia tych wymagań.
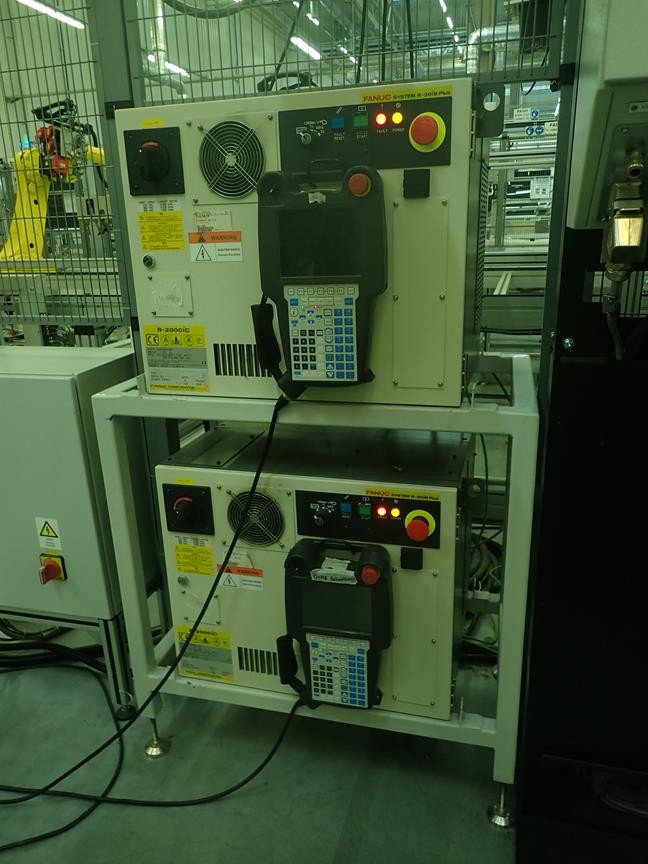
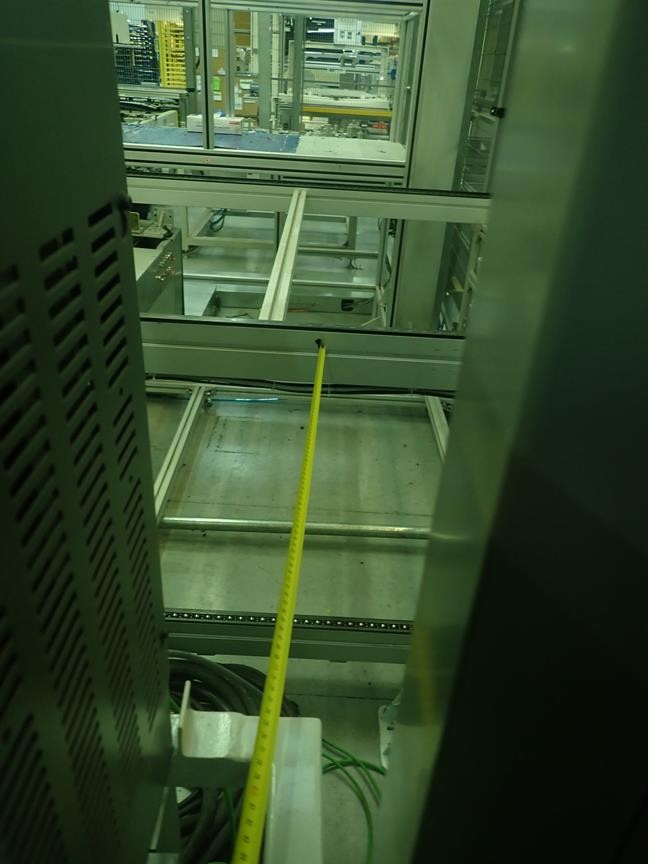
Widoczność
Norma PN-EN ISO 14118 określa różne sposoby i możliwości zapobiegania niespodziewanemu uruchomieniu maszyny. Jednym z nich jest wymóg resetowania wszystkich funkcji bezpieczeństwa po ich aktywacji. Wycofanie grzybka e-stop lub zamknięcie bramki serwisowej nie może samo w sobie spowodować uruchomienia maszyny. Unikając przypadkowości wymaga się świadomego działania — wciskając ręczny reset.
Co łączy widoczność i funkcję reset? Z każdego stanowiska sterowania operator powinien mieć możliwość upewnienia się, że nikt nie znajduje się w chronionej przestrzeni. Analogicznie do przysłowia o wychowywaniu dzieci możemy powiedzieć — mała strefa mały problem, duża strefa duży problem. Jeśli pełnej widoczności nie da się osiągnąć, stosuje się właśnie reset.7 Resetując, musimy mieć przede wszystkim pewność, że nikt nie został w strefie zrobotyzowanej.
W przypadku linii zrobotyzowanych, gdzie nie możemy osiągnąć pełnej widoczności strefy niebezpiecznej, ciekawym — acz droższym — rozwiązaniem jest zapewnienie dodatkowych środków ochronnych w postaci urządzeń wykrywających obecność, np. skanerów bezpieczeństwa. Dla aplikacji o słuszniejszych rozmiarach, gdzie pełna widoczność jest praktycznie niemożliwa do osiągnięcia, możemy zastosować wizualne oraz dźwiękowe sygnały ostrzegawcze. Sygnalizacja poprzedza start maszyny, a czas trwania ostrzeżenia powinien być wystarczający, aby umożliwić operatorowi (-om) skorzystanie ze środków zapobiegających uruchomieniu maszyny lub bezpieczne opuszczenie chronionego obszaru.
cdn.
W tej serii:
1. Układ aplikacji z robotem.
2. Tryby pracy.
3. Zapewnienie poziomu bezpieczeństwa.
﹏﹏﹏
- https://ifr.org/[⤣]
- Miałoby to również ogromne uzasadnienie chociażby w kontekście urzędnicy vs. przedsiębiorcy.[⤣]
- Integrated Manufacturing System[⤣]
- przestrzeń chroniona i ograniczona robota zostały omówione w artykule na temat audytu celi zrobotyzowanej[⤣]
- PN-EN ISO 13857, 4.3[⤣]
- 8.5.2[⤣]
- Na stanowiskach zrobotyzowanych reset jest wymagany nawet przy pełnej widoczności, zgodnie z ISO 10218-2, 5.6.3.4.2.[⤣]
Dodaj komentarz